Best Practice
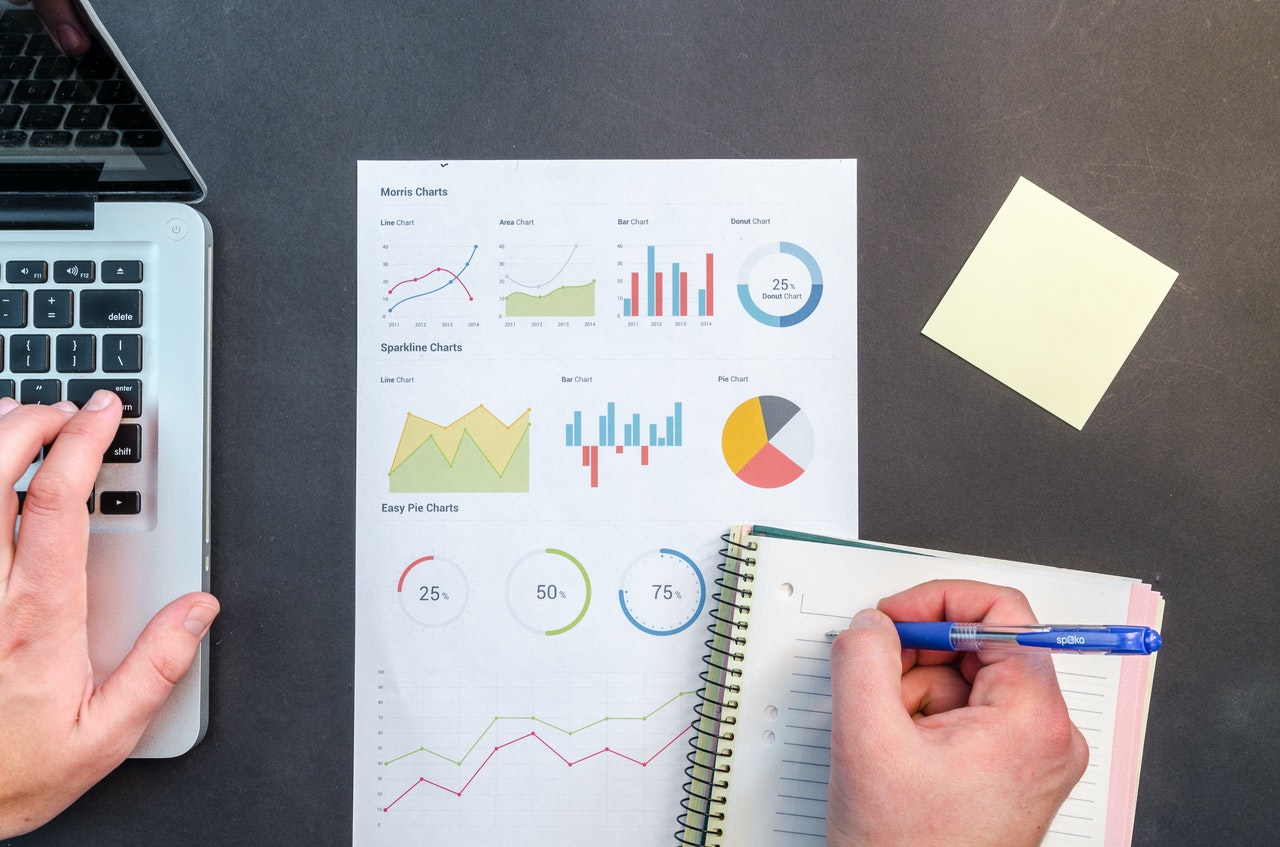
Die Mitgliedsunternehmen des TECHNOS e. V. sind sehr an gemeinsamen Forschungsprojekten interessiert. Die sich durch die unterschiedlichen Blickwinkel ergebenden Synergien haben schon häufig zu neuen und erfolgversprechenden Ergebnissen und Zusammenarbeiten geführt.
Gerne informieren wir Sie über aktuelle öffentlich geförderte Forschungsprogramme.
Hier sehen Sie Beispiele gelungener Forschungskooperationen:
Forschungsprojekte in Kooperation mit TECHNOS e. V. – Unternehmen
Laufende Projekte
topAM
Bei dem im Rahmen des EU-geförderten Spire 2030 Programms geförderten Projekt geht es darum, die nachhaltige Prozessindustrie durch Ressourcen- und Energieeffizienz voranzutreiben.
Zusammen mit industriellen Partnern aus 6 europäischen Ländern soll in diesem interdisziplinären Projekt neuartige ODS- (oxid-particle-dispersoid strengthened) Hochtemperaturlegierungen entwickelt werden, die mittels additiver Fertigung verarbeitet werden können und in aggressiven Hochtemperaturumgebungen zum Einsatz kommen können. Dadurch soll die Prozesskette bei der Herstellung von Gasbrennerköpfen und Wärmetauschern verkürzt und optimiert werden, um eine erhöhte Lebensdauer dieser Teile im Einsatz zu ermöglichen. Durch die Verbindung von ICME (integrated computational material engineering) und additiver Fertigung mit selektiven Laserschmelzens sollen einzigartige Materialeigenschaften erzielt werden.
InnoMat3D
Ziel der ersten einjährigen Phase des Innovationsnetzwerks ist neben der Entwicklung von Projektideen und der Erarbeitung einer technologischen Roadmap, die Akquise von weiteren Partnern, welche die Kompetenzen des Netzwerks ergänzen.
Bei Interesse an der Mitwirkung im Netzwerk nehmen Sie bitte Kontakt zur Netzwerkmanagerin Dr. Katrin Jahns auf.
Förderung
Europäischer Fond zur Regionalen Entwicklung (EFRE)
E-Mat3D
Buchsenkontakt des TC-200 Stecker der Firma Harting
Entwicklung neuer Kupferwerkstoffe für die Additive Fertigung von Hochleistungsbaustoffen für die Elektromobilität
Partner: KME Germany, Harting Technologiegruppe
Gesamtvolumen: 311.000 €
Projektlaufzeit: 01.12.2019 – 30.11.2022
Aktuelle Informationen zu E-Mat3D finden Sie auf der Seite Neuigkeiten.
Abgeschlossene Projekte
KombiMat3D
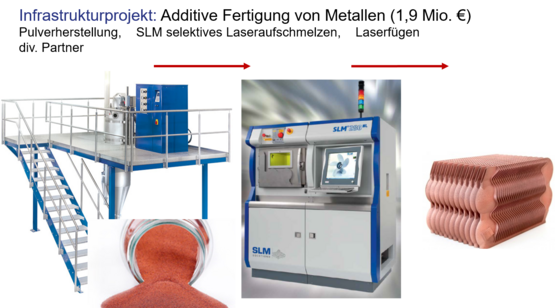
Die Hochschule Osnabrück erhält mehr als 1,6 Millionen Euro Fördermittel, um Anlagen für die additve Fertigung zu beschaffen.
Das Team der Forscherinnen und Forscher um Prof. Dr. Ulrich Krupp freut sich über das bewilligte Infrastrukturprojekt „Kombiniertes Material- und Produktdesign durch additive Fertigungsverfahren – Technologiecampus 3D-Werkstoffdesign (KombiMat3D)“ und sieht spannenden Aufgaben entgegen. Erste Folgeprojekte mit industrieller Beteiligung sind bereits geplant. Das TECHNOS-Netzwerk wird sich auch hier einbringen.
Ohne Umwege von der Idee zum Produkt – die additive Fertigung ermöglicht die endkonturnahe, werkzeuglose Umsetzung fast beliebiger dreidimensionaler-Geometrien. Komplex geformte biomedizinische Implantate, mit Kühlkanälen durchdrungene Hochleistungswerkzeuge, Ersatzteile on demand – die Gerätetechnik zum 3D-Drucken befindet sich in einem rasanten Entwicklungsprozess. Neben thermoplastischen Polymeren, die in einem Druckkopf extrudiert und ähnlich einem Tintenstrahldrucker in 3D aufgespritzt werden, können Metalle schichtweise in einem Pulverbett aufgeschmolzen werden und so zu einer 3D-Struktur aufgebaut werden.
Die sogenannte SLM-Technik (selective laser melting) wird im Rahmen einer Forschungsinfrastruktur-Initiative der EU und des Landes Niedersachsen (Umfang: ca. 1,9 Mio. Euro) gemeinsam mit einem System zur Herstellung neuer Metallpulver und einer robotergestützten Laser-Fügeanlage ab 2018 auf einem neuen Außenstandort der Hochschule Osnabrück in einer eigenen Industriehalle aufgebaut und für Transfer- Projekte mit regionalen Industrieunternehmen im TECHNOSNetzwerk zur Verfügung stehen.
Der Technologiecampus soll die Wertschöpfungskette moderner Fertigungstechnik zur 3D-Umsetzung von der Idee, über das CAD-Modell, virtuelle Dimensionierung bis zur Eigenschaftsprüfung von Prototypen abbilden. In dem eigens eingerichteten Technikum erarbeiten Studierende, Designer und Konstrukteure und Wissenschaftler maßgeschneiderte Lösungen für neue Produktideen. Flankiert durch das Unternehmensnetzwerk TECHNOS (Technologiezentrum Neue Materialien Osnabrück- Emsland) soll der Forschungscampus zu einem erfolgreichen Transfer neuer Fertigungsmöglichkeiten mit Rückkopplung in multidisziplinäre, innovative Lehransätze durch
• Fortbildungen, Workshops und Trainings,
• Planung und Fertigung von Prototypen,
• Charakterisierung und Prüfung von Werkstoff- und Bauteileigenschaften,
• Ideen-Börsen mit Schülern, Studierenden und Professionals.
Kooperationspartner: Fraunhofer-Institut für Angewandte Materialforschung IFAM (Dresden), Fraunhofer-Institut für Werkzeugmaschinen und Umformtechnik IWU (Chemnitz), Institut für Werkstofftechnik der Universität Kassel, Laser Zentrum Nord (Hamburg), Krause DiMaTec (Bielefeld), Zoz GmbH (Wenden), MEMA-Netzwerk in der Emsland GmbH Meppen, KME Germany GmbH und Co. KG, Hochschule Osnabrück
Weitere Informationen hier.
Metform
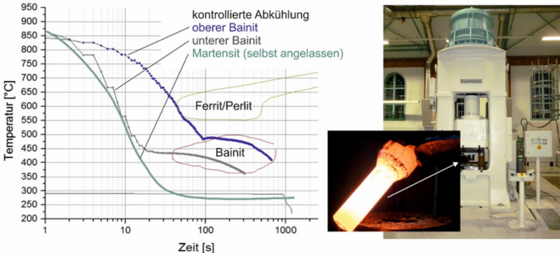
Umformsimulation zum virtuellen Design metallischer Hochleistungswerkstoffe (Metform)
Die hohe Effizienz, mit der heutzutage Werkstoffe produziert und verarbeitet werden, wird maßgeblich durch die zunehmende Digitalisierung industrieller Fertigungsprozesse erreicht.
Im Rahmen des Projekts Metform wird ein Werkstoffprozesssimulator angeschafft, mit dessen Hilfe die exakte Abbildung realer Fertigungstechnologien gelingt und gleichzeitig benötigte Kennwerte zum virtuellen Design von Produktionsprozessen, wie bspw. das temperaturgeregelte Walzen oder das Warmfließpressen, für metallische Hochleistungswerkstoffe generiert werden können.
Werkstoffe 4.0: Von der Gefügesimulation zum neuen Werkstoff Eine ressourcenschonende und effiziente Wertschöpfungskette im großindustriellen Maßstab, wie bspw. die Walzprozesse bei den Projektpartnern Georgsmarienhütte Stahl oder KME Germany, erfordert ein tiefgreifendes Verständnis der Mikrostrukturveränderungen während der individuellen Prozessschritte.
Mit Hilfe moderner computergestützter Rechenmodelle für die Werkstoffsimulation können heute diese Mikrostrukturveränderungen und die daraus resultierenden mechanisch-technologischen Eigenschaften vorausberechnet werden. Grundvoraussetzung dafür ist die Verfügbarkeit genauer Werkstoffdaten. Sind diese als Eingangsgrößen bekannt, ist die Modellierung der Wechselwirkung zwischen Fertigungsprozess und physikalischen/ technologischen Eigenschaften des Werkstücks möglich. Mit Hilfe einer durchgehenden Prozessdatenerfassung, wie bspw. Umformkräfte und -temperaturen, können die Modelle kontinuierlich angepasst werden.
So erlaubt „Big Data“ aus der fertigungsbegleitenden Messtechnik die Korrelation von Prozessabweichungen, wie z. B. Variationen in der chemischen Zusammensetzung, mit der Variationsbreite der Werkstoffeigenschaften und ermöglicht so eine zielgerichtete und schnelle Weiterentwicklung der Werkstoffprozesstechnik und der Qualitätssicherung.
Kooperationspartner:
- Hochschule Osnabrück
- Georgsmarienhütte Stahl
- KME Germany GmbH & Co. KG
- MBH Maschinenbau & Blechtechnik GmbH
Weitere Informationen hier.
Dubio
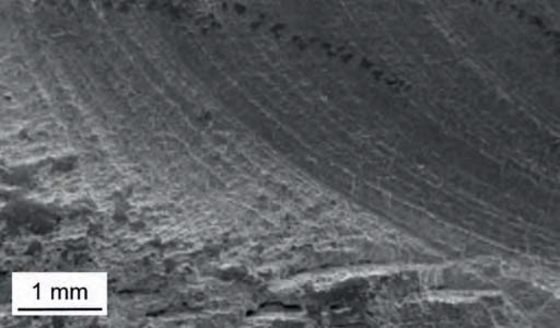
Einsatzgruppen von Duplexstählen für bioverfahrenstechnische Anlagen
Duplexstähle weisen nicht nur eine hohe Ermüdungsfestigkeit auf, sondern zeigen auch gute Korrosionsbeständigkeit, was sie für den Einsatz in der Verfahrenstechnik, im Offshorbereich und für andere Anwendungen geeignet macht. Unter bestimmten korrosiven Bedingungen reduziert sich allerdings die Lebensdauer dieser Stähle. Untersuchungen haben gezeigt, dass dies vermutlich durch Schwingungsrisskorrosion bedingt ist und die korrosive Wirkung von Salznebel einen erhöhten Anteil an gebrochenen Gleitbändern bewirkt. Duplexstähle sind gut schweißbar und die Schweißnähte sind als Bauteilverbinder oft besonders belastet. Durch ihr verändertes Gefüge wird auch der Widerstand gegenüber Schwingungsrisskorrosion beeinflusst.
Es werden daher aus X2CrNiMoN22-5-3 (1.4462) Proben aus dem Grundwerkstoff , sowie aus Schweißgut untersucht, wobei sowohl die Schweißnaht selbst, als auch die Wärmeeinflusszone betrachtet werden. Dazu wurde eine Prüfkammer entwickelt, in der die Proben in einem Salznebel nach DIN EN ISO 9227 mittels Ultraschall-Ermüdungstechnik belastet werden und somit den Einfluss des Umgebungsmediums auf die Dauerschwingfestigkeit reproduzierbar bestimmt werden kann.
Neben der Untersuchung der Dauerschwingfestigkeit werden die Bruchflächen und ermüdeten Oberflächen (elektronen-)mikroskopisch untersucht, um weitere Hinweise auf die Wirkung des Salznebels zu erhalten.
Projektleitung:
Prof. Dr.-Ing. habil. Ulrich Krupp
Prof. Dr.-rer. nat. Angela Hamann-Steinmeier
Dr.-Ing. Javad Mola
Kontakt:
Prof. Dr.-Ing. habil. Ulrich Krupp
IEHK-Institut für Eisenhüttenkunde/Steel Institute
RWTH Aachen University
Intzestraße 1
D-52072 Aachen
Telefon: +49 241-8092913
E-Mail: krupp@iehk.rwth-aachen.de
Frau Dr. rer. nat. Angela Hamann-Steinmeier
Laborbereich Biologische Verfahrenstechnik
Hochschule Osnabrück-University of Applied-Sciences
Albrchtstraße 30
D-49076 Osnabrück
Telefon: +49 541-969-2902
E-Mail: a.hamann@hs-osnabrueck.de
Herr Dr. Javad Mola
Laborbereich Materialdesign und Werkstoffzuverlässigkeit (hier…)
Hochschule Osnabrück-University of Applied Sciences
Albrechtstraße 30
D-49076 Osnabrück
Telefon: +49 541-969-2188
E-Mail: j.mola@hs-osnabrueck.de
Kooperationspartner:
Wilhelm Niemann GmbH & Co.
Nordlandstraße 16
D-49326 Melle
Wissenschaftlicher Mitarbeiter:
M.Sc. Jan-Stefan Peters
Projektdauer:
12/2017-11/2019
Finanzierung:
Europäischer Founds für regionale Entwicklung (EFRE)
Weitere Informationen hier.
HochSeil
Quantitative Analyse und Optimierung der Fertigungsprozesse für hoch beanspruchte Stahlseile
Die technologische Optimierung von Werkstoffen beschränkt sich nicht nur auf die metallurgische Weiterentwicklung des Werkstoffs, sondern bedarf auch eine ganzheitliche Betrachtung des Produktions- und Verarbeitungsprozesses. Im Rahmen des vorliegenden Forschungsvorhabens „HochSeil“ erfolgt eine solche ganzheitliche Untersuchung der Herstellung und Verarbeitung von hochfesten Drahtseilprodukten für den Bau von Brückenbauwerken, Förder- und Hebesystemen und im Bereich von Mobilitätsprodukten.
Ein besonderes Verfahren der thermomechanischen Behandlung von Stählen stellt das Bleipatentieren von Drähten dar, dass der Projektpartner Vornbäumen Draht GmbH & Co.KG. zur Herstellung hochfester Stahlseile einsetzt. Durch den Prozess des Patentierens lassen sich sehr hohe Festigkeiten von Re>2000MPa erzielen. Um diese für eine optimierte Fertigung sicherheitsrelevanter Seilanlagen voll ausnutzen zu können, ist eine präzise Kenntnis der Prozessparameter und deren Einfluss auf die mechanisch-technologischen Eigenschaften erforderlich. Forschungsschwerpunkt soll hierbei die quantitative Ermittlung der Einflüsse der Prozessparameter, wie zum Beispiel dem Umformgrad, die Austenitisierungstemperatur oder der isothermen Haltedauer, sowie den Einflüssen der einhergehenden Mikrostruktur des Werkstoffs sein. Resultierend aus den empirischen Erkenntnissen werden entsprechende Schädigungsmechanismen adaptiert und weiterentwickelt. Auf Basis dieser entwickelten Schädigungsmechanismen und Eigenschaftsbeziehungen erfolgt die technologische Optimierung des Herstellungs- und Verarbeitungsprozesses.
Projektleitung:
Prof. Dr. Ing. habil. Ulrich Krupp
Dr.-Ing. Javad Mola
Prof. Dr.-Ing. Bernhard Adams
Kontakt:
Labor Materialdesign und Werkstoffzuverlässigkeit (hier…)
Hochschule Osnabrück
Albrechtstraße 30
D-49076 Osnabrück
Tel. +49 541-969 2188
j.mola@hs-osnabrueck.de
Kooperationspartner:
Vornbäumen GmbH & Co.KG.
Wissenschaftlicher Mitarbeiter:
Kevin Koschella, M.Sc.
Nooshin Bandari, M.Sc.
Projektddauer:
12/2018-12/2020
Weitere Informationen hier.
SimkoSteel
Modellierung und Simulaion der Hochtemperaturaufkohlung für dynamisch beanspruchte Hochleistungsstähle
Um hochbeanspruchte Bauteilen wie Zahnrädern und Getriebebauteilen gute Gebrauchseigenschaften zu verleihen, wird das Verfahren des Einsatzhärtens verwendet. Beim Einsatzhärten wird zu diesem Zweck die Randschicht des Stahls mit Kohlenstoff angereichert, was bei der asnchließenden Härtung zu einer entsprechend hohen Festigkeit führt. Ein weiteres Ziel der Einsatzhärtung ist neben der Erhöhung von Härte und Verschleißbeständigkeit die Steigerung der Schwingfestigkeit über das Einbringen von Druckeigenspannungen in die Bauteiloberfläche. Beim Niederdruckaufkohlen unter einem Druck von 5 bis 30 mbar tritt eine beschleunigte Zerfallsreaktion der Aufkohlungsgase auf, die zu einem geringeren Gasverbrauch, sowie einer geringeren Randoxidation führt [1].
Insgesamt ist das Einsatzhärten ein zeit- und energieintensives Verfahren, wobei durch eine Erhöhung der Aufkohlungstemperatur die Behandlungsdauer deutlich verkürzt werden kann. Üblich sind Aufkohlungstemperaturen von 850°C – 950°C. Die Verwendung von Temperaturen von 1000°C können zu einer Zeitersparnis von mehr als 50% führen [2]. Allerdings besteht bei höheren Temperaturen das Risiko der Kornvergröberung, so dass die Feinkornbeständigkeit des Materials im entsprechenden Temperaturbereich für eine erfolgreiche Einsatzhärtung entscheidend ist.
Durch den Einsatz der Phasenfeldmethode gelingt es, die Wachstumskinetik von Zweit- und Drittphasen, sowie Körnern während der Erstarrung von Schmelzen, aber auch in Festkörpern realitätsnah abzubilden. Das verhältnismäßig neue Softwareprodukt MICRESS nutzt die Phasenfeldmethode in Kombination mit der leistungsfähigen datenbankgestützten Thermodynamiksoftware ThermoCalc, um die Kornvergröberung während der Aufkohlung zu simulieren. Dies ist für das hier beschriebene Projekt von besonderem technologischen Interesse, da auch das Korngrenzenpinning durch Ausscheidungen in Anwesenheit von Mikrolegierungselementen berücksichtigt werden kann (vgl. [3, 4]). Die VHCF-Versuche dienen des Schwingungsfestigkeitsnachweises für die aufgekohlten und carbonitrierten Varianten des Stahls mit Hilfe einer Ultraschallprüfmaschine (Typ BOKU) bei einer Frequenz von f=20.000Hz.
Abschließend muss die Simulation in der Lage sein, die Gefügestruktur und die Einsatzhärtetiefe verlässlich vorherzusagen. Die Simulation kann in Zukunft sowohl zur erfolgreichen virtuellen Materialentwicklung, als auch zur Prozessentwicklung eingesetzt werden.
[1] D. Liedke: Stand des Einsatzhärtens aus industrieller Sicht, HTM Journal of Heat Treatment and Materils, 64 (2009) 323
[2] B. Clausen, S. Konovalov, F. Hoffmann, U. Prahl, H.-W. Zoch, W. Bleck: Feinkornbeständigkeit von Bauteilen aus dem mikrolegierten Werkstoff 18CrNiMo7-6 in Abhängigkeit der Prozesskette, HTM Journal of Heat Treatment an Materials, 5 (2010) 257
[3] J. Rudnizki, B. Zeislmair, U. Prahl, W. Bleck: Prediction of Abnormal Grain Growth during High Temperature Treatment, Computational Materials Science, 49(2) (2010) 209
[4] M. Apel, B. Böttger, J. Rudnizki, P. Schaffnit, I. Steinbach: Grain Growth Simulations including Particle Pinning using the Multiphase-Field Concept, ISIJ International. 49(7) (2009) 1024
Projektleitung:
Prof. Dr.-Ing. habil. Ulrich Krupp
Dr. Ing. Javad Mola
Prof. Dr.-Ing. Jürgen Wübbelmann
Kontakt:
Herr Prof. Krupp
IEHK-Institut für Eisenhüttenkunde/Steel Institute
RWTH Aachen University
Intzestraße 1
D-52072 Aachen
Telefon +49 241-8092913
krupp@iehk.rwth-aachen.de
Herr Dr. Mola
Laborbereich Materialdesign und Werkstoffzuverlässigkeit (hier…)
Hochschule Osnabrück-University of Applied Sciences
Albrechtstraße 30
D-49076 Osnabrück
Telefon: +49 541969-2188
j.mola@hs-osnabrueck.de
Herr Prof. Dr.-Ing. Wübbelmann
Betriebssysteme und Embedded Systems
Hochschule Osnabrück-University of Applied Sciences
Albrechtstraße 30
D-49076 Osnabrück
Telefon: +49 541969-7008
Kooperationspartner:
Stahlwerk Georgsmarienhütte GmbH
Hanomag Lohnhärterei GmbH
Wissenschaftlicher Mitarbeiter:
Sayantan Sarkar, M.Sc.
Projektdauer:
01/2018 – 12/2019
Finanzierung:
Europäischer Founds für regionale Entwicklung (EFRE)
Weitere Informationen hier.
OptiHeat
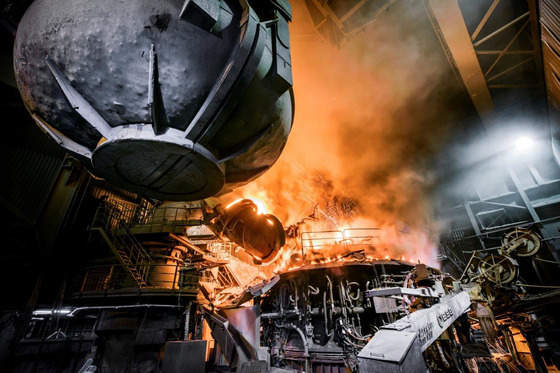
Optimierung von Umform- und Wärmebehandlungsprozessen für eine wirtschaftliche und anwendungsorientierte Gestaltung von Hochleistungswerkstoffen
Der von 2013 bis 2019 an der Hochschule Osnabrück etablierte Forschungsschwerpunkt zielt auf die Entwicklung einer Methodik, mit der sich Wärmebehandlungsverfahren mit den Fertigungsprozessen derart abstimmen lassen, so dass eine deutliche Verkürzung der Prozessdauer bei gleichzeitiger Verbesserung der mechanischen Eigenschaften erreicht wird.
Ausgangspunkt sind dabei konkrete Aufgabenstellungen der Industriepartner, darunter die thermomechanische Behandlung von Nickelbasis-Superlegierungen und bainitischen Stählen.
Der Forschungsschwerpunkt zielt auf die Entwicklung einer Methodik, mit der sich Wärmebehandlungsverfahren mit den Fertigungsprozessen für Konstruktionswerkstoffe derart abstimmen lassen, dass eine deutliche Reduktion der Prozessdauer bei gleichzeitiger Verbesserung der mechanischen Eigenschaften erreicht werden. Ausgangspunkt sind dabei konkrete Problemstellungen der Industriepartner, die bereits in kleineren Entwicklungsprojekten beleuchtet werden konnten.
Bei den im Projekt untersuchten Werkstoffen handelt es sich um bainitische Stähle, die beispielsweise in Common-Rail-Systemen verbaut werden und um hochtemperaturbeständige Nickelbasislegierungen, welche im Turbinenbau zu finden sind.
Die Hochschule Osnabrück verfügt über eine 10.000kN Spindelpresse und kann somit nahezu den gesamten Fertigungsprozess abbilden. Die Abbildung zeigt das experimentelle Vorgehen am Beispiel des bainitischen Stahls: Zunächst werden Prüfkörper geschmiedet und gezielt abgekühlt. Anschließend werden die Eigenschaften mittels Metallographie (u.a. analytischer Elektronenmikroskopie) und mechanischer Werkstoffprüfung charakterisiert.
Neben den experimentellen Arbeiten, spielt die Modellierung eine immer größere Rolle bei der Optimierung von Prozessen. Hierbei wird sowohl der Schmiedeprozess als auch die komplexe Ausscheidungskinetik der Werkstoffe berücksichtigt.
Die Kombination von Umformsimulation (SimuFact), Finite-Elemente-Berechnungen der Abkühlung und schließlichder Einbeziehung von Kinetik und Thermodynamik der Ausscheidungsbildung (MatCalc) soll dazu beitragen, die Prozessparameter für die vielfältigen Werkstoffanforderungen bereits im Vorfeld festlegen zu können.
Projektleitung
Prof. Dr.-Ing. habil. Ulrich Krupp
Dr.-Ing. Javad Mola (Nachfolgevertretung)
Prof. Dr.-Ing. Wilhelm Michels
Prof. Dr.-Ing. Bernhard Adams
Prof. Dr.-Ing. Jürgen Wübbelmann
Prof. Dr.-Ing. Alexander Schmehmann
Kontakt
Herr Prof. Krupp
IEHK-Institut für Eisenhüttenkunde / Steel Institute
RWTH Aachen University
Intzestraße 1
D-52072 Aachen
Telefon: +49 241-8092913
krupp@iehk.rwth-aachen.de
Herr Dr. Javad Mola
Laborbereich Materialdesign und Werkstoffzuverlässigkeit
Hochschule Osnabrück-University of Applied Sciences
Albrechtstraße 30
D-49076 Osnabrück
Telefon: +49 541 969-2188
j.mola@hs-osnabrueck.de
Wissenschaftliche Mitarbeiter
Dr. rer. nat. Christine Derks
M. Sc. Anne Hesselink
M. Sc. Mikhail Solovev
Kooperationspartner
Georgsmarienhütte GmbH (Hauptpartner)
MAN Diesel & Turbo SE
Aubert Duval (Eramet)
Siemens Energy AG
Projektdauer
03/2013-06/2019
Finanzierung
Niedersächsisches Ministerium für Wirtschaft und Kultur, MWK (ursprünglich gefördert durch die Arbeitsgruppe Innovative Projekte (AGIP))
Veröffentlichungen
Artikel in Fachzeitschriften:
A. Hesselink, J.-M. Tiemann, M. Solovev, U. Krupp, Influence of the y´Phase on the Creep Behavior of a New Polycrystalline Nickel-Based Superalloy (AD 730), PM54(2017) 838-848
Konferenzbeiträge:
A. Hesselink, J.-M. Tiemann, M. Solovev, U. Krupp, Einfluss der g`- Phase auf das Kriechverhalten einer neuen polykristallinen Nickelbasis-Superlegierung (AD730), in: 50. Metallographie-Tagung, 21-23. September 2016, Berlin
M. Solovev, J.-M. Tiemann, A. Hunfeld, C. Derks, B. Adams, U. Krupp, W. Michels, Influence of Hot-Extrusion on Microstructure and High-Temperature Properties of a new Nickel Based Superalloy (AD730) in: MSE-Materials Science and Engineering Congress, 27.-29. September 2016, Darmstadt
A. Hesselink, J.M. Tiemann, M. Solovev, B. Adams, U. Krupp, Influence of a thermomechanical treatment on g`-precipitates and the creep behavior of the new nickel base superalloy AD730, in: Euromat, 17.-22. September 2017, Thessaloniki, Griechenland
A. Hesselink, S. Walter, M. Harwarth, U. Krupp, Microstructure and creep / dwell-time fatigueproperties of a hot extruded superalloy (AD730), in: MSE-Materials Science and Engineering Congress, 26.-28. September 2018, Darmstadt
A. Hesselink, S. Walter, M. Harwarth, U. Krupp, Einfluss einer thermomechanischen Behandlung auf die Hochtemperaturfestigkeitseigenschaften der neuen polykristallinen Nickelbasis-Superlegierung AD730. in: 36. Tagung Werkstoffprüfung 2018, 6.-7. Dezember 2018, Bad Neuenahr
Weitere Informationen hier.
Analyse des Leichtbaupotentials landwirtschaftlicher Maschinen
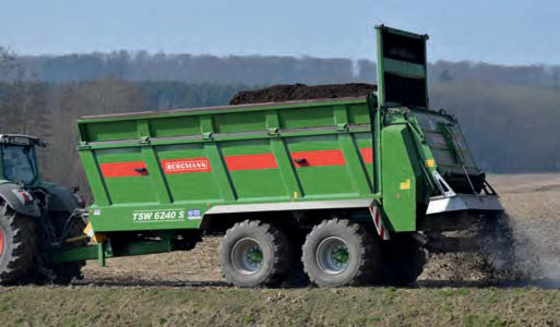
Entwicklungsprojekt gefördert durch den Europäischen Fonds für regionale Entwicklung, EFRE
Das seit Oktober 2016 laufende Forschungsprojekt verfolgt die Charakterisierung und Nutzbarmachung moderner Werkstoff- und Fügetechnologien für eine neue Generation gewichts- und funktionsoptimierter landwirtschaftlicher Maschinen anhand einer Baugruppe des Partnerunternehmens Ludwig Bergmann GmbH.
In der Landtechnik werden analog zur Automobilindustrie zunehmend hoch- und höchstfeste Stähle für Leichtbaulösungen eingesetzt.
Darüber hinaus zeichnet sich auch in der Landtechnik aus wirtschaftlichen, aber auch aus funktionellen Gründen ein Bedarf an maßgeschneiderten Leichtbaukonzepten ab.
Der Einsatz höherfester Werkstoffe erlaubt nicht nur eine Gewichtsreduktion, sondern bei geschickter Wahl der Werkstoffe und der zugehörigen Prozess- und Fügetechnik auch eine Erhöhung der Verschleißbeständigkeit.
Kooperationspartner:
- Ludwig Bergmann GmbH
- Hochschule Osnabrück
Weitere Informationen hier.